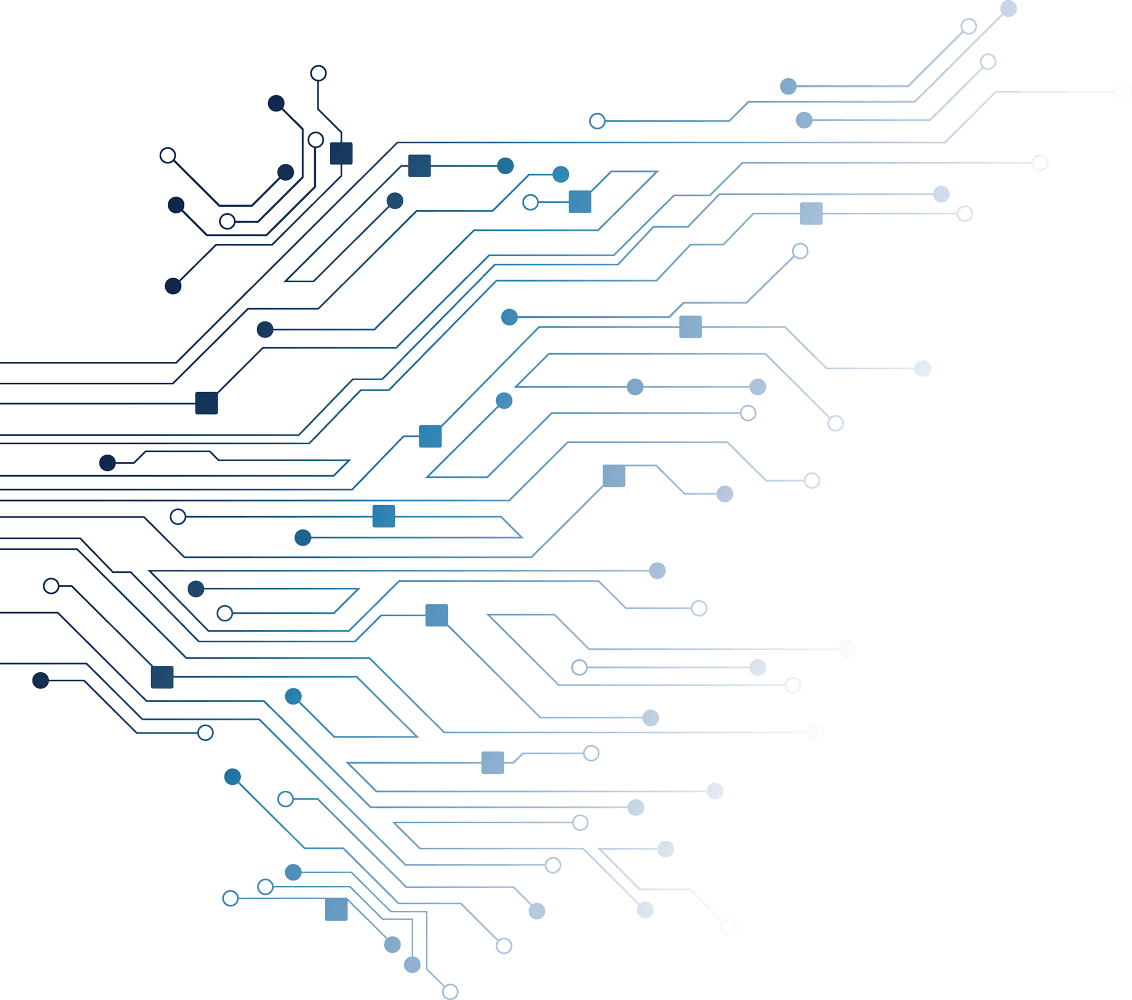
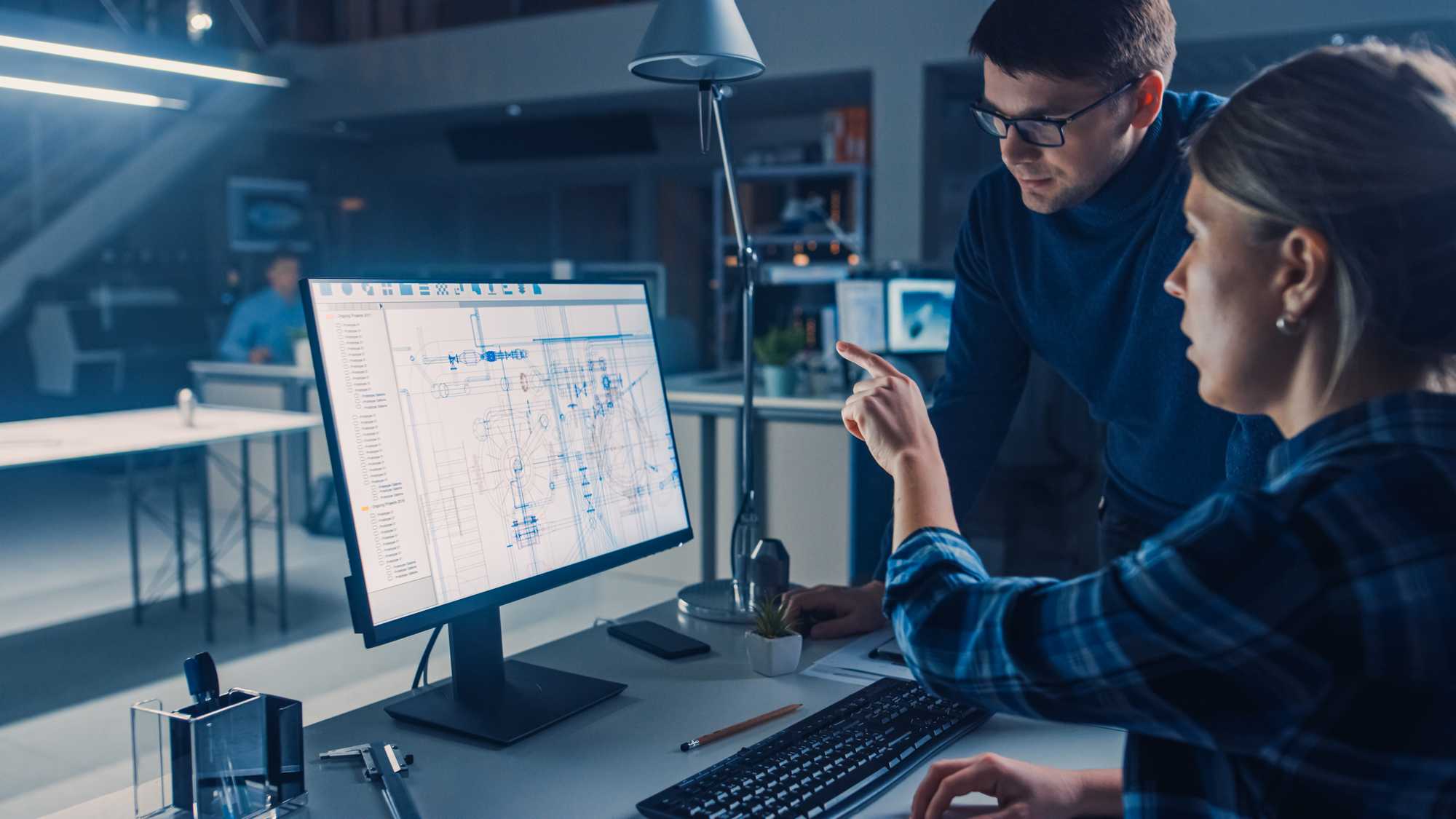
Experienced Company
We adapt our delivery to the way your work, whether as an external provider.
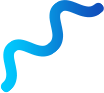
Design Development
Products and prototypes in your hands in few weeks
We are passionate about using innovative technologies for 3D printing and additive manufacturing to be able to respond to the needs of clients and the ever-changing demands of markets.
Our experienced designers and engineers uphold our commitment to be specialists in a range of new and evolving technologies. Our client satisfaction oriented approach maintains our ability to provide our customers with high quality outputs at the lowest possible cost.
Rhino/Grasshopper
Fusion360
Maya, Blender, ZBrush
3D printing
Materialize your ideas
Mirage 3D Printing Service allows you to order a prototype or series of functional parts fast using state of art technologies such as FDM or SLA. Select from materials below and upload your 3d file NOW for an express quote.
of expertise in additive manufacturing for production and prototyping
Max part size 500x500x600 mm Layer 100-300 um
Fused deposition modeling combines a specific form of design with 3D printing and fast delivery times with production-grade thermoplastics to create durable parts with excellent mechanical properties. The technology is ideal for functional prototypes, durable production tools and low-volume final parts, and is suitable for aerospace and other industries that rely on certified manufacturing.
Max part size 270x150x400 mm Layer 50um
Stereolithography is a preferable technology for its ability to process widest design features. Its surface quality, ability to keep fine details and wide range of materials make it ideal for superior models and prototypes, complex parts, and prototypes for techniques like vacuum forming. See Materials section for more details
Customer satisfaction
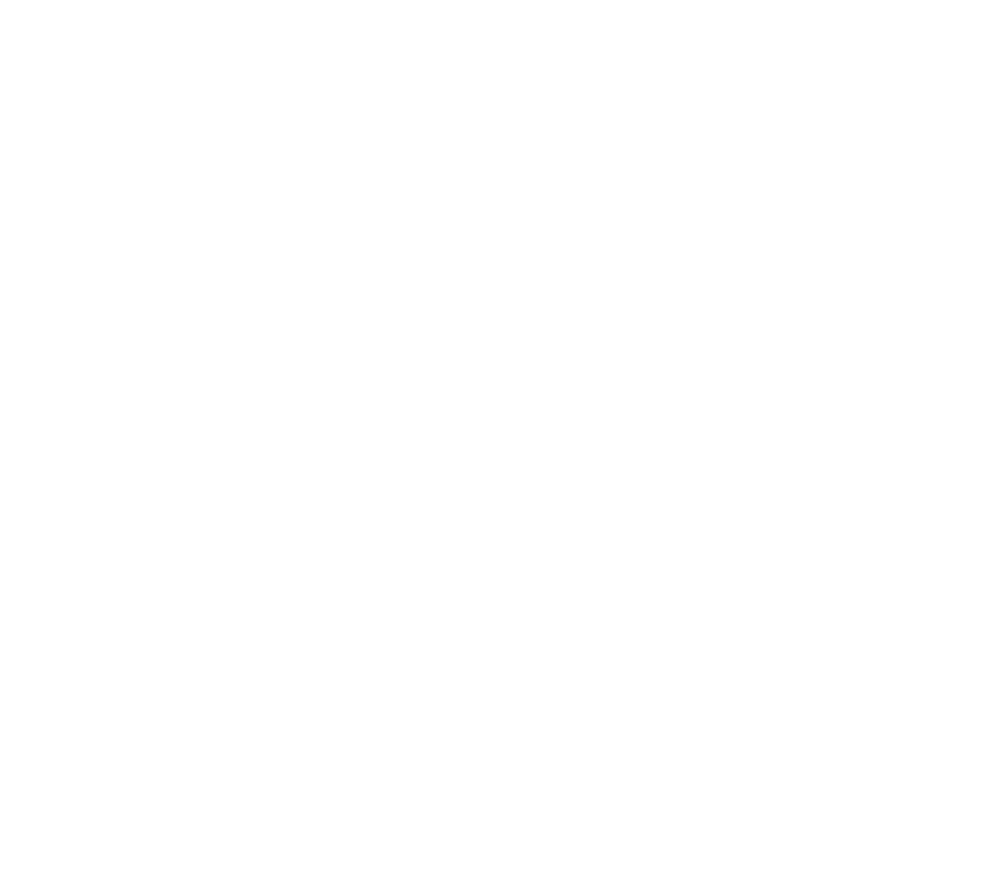
THERMOFORMING
Fast and efficient series manufacturing
No alternative process can match the low cost, ease of tooling, efficiency and speed of replication for prototyping and small series of certain shapes. One of the main benefits of vacuum forming is the speed at which tooling can be produced and the cost compared to injection moulding is substantially cheaper.
Combining vacuum forming with new technologies such as 3D printing for tool design, thermo-formable ink technology and In-Mould Decoration bring new possibilities and advantages.
Vacuum forming offers several processing advantages over other forming processes. Low forming pressures are used thus enabling comparatively low cost tooling.
Since the process uses low pressures, the molds can be made of inexpensive materials and mold fabrication time can be reasonably short. Prototype and low quantity requirements of large parts, as well as medium size run therefore become economical. More sophisticated machines and molds are used for continuous automated production of high volume items (yoghurts pots…).
Vacuum forming uses extruded plastic sheet and a secondary process may be required to trim the formed sheet to arrive at the finished part.
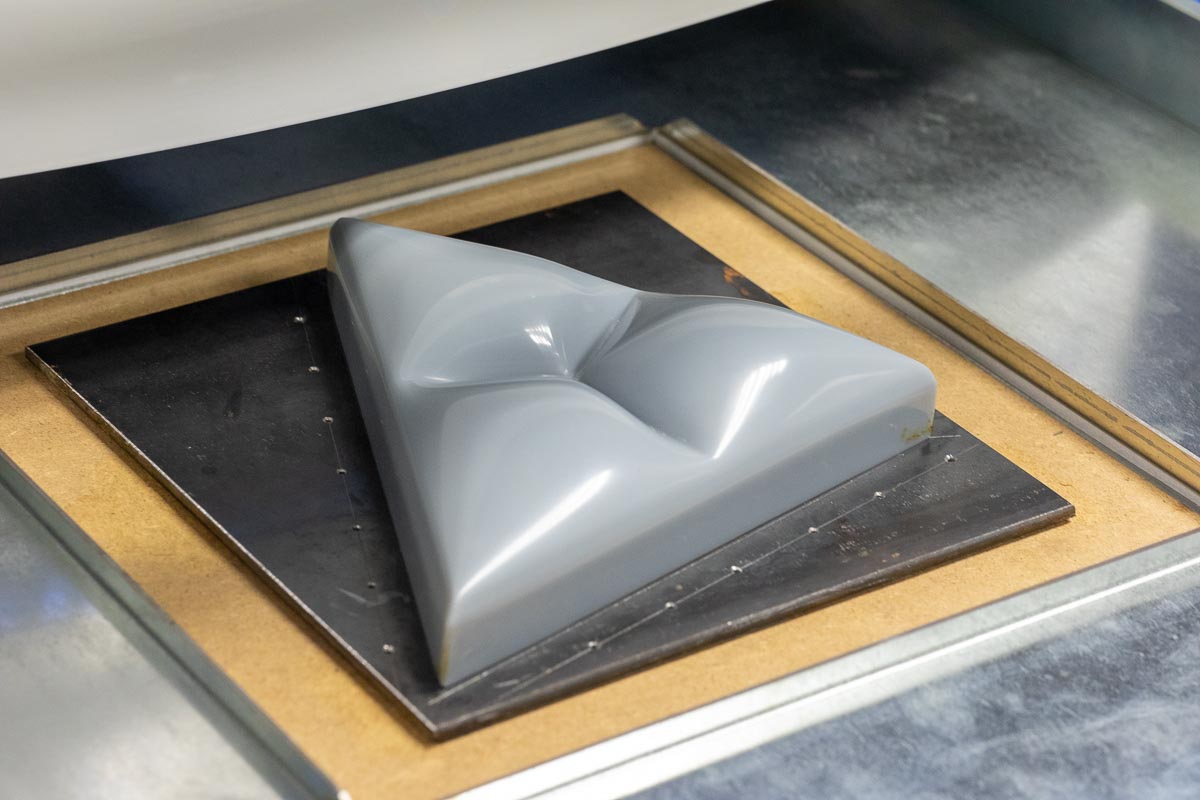
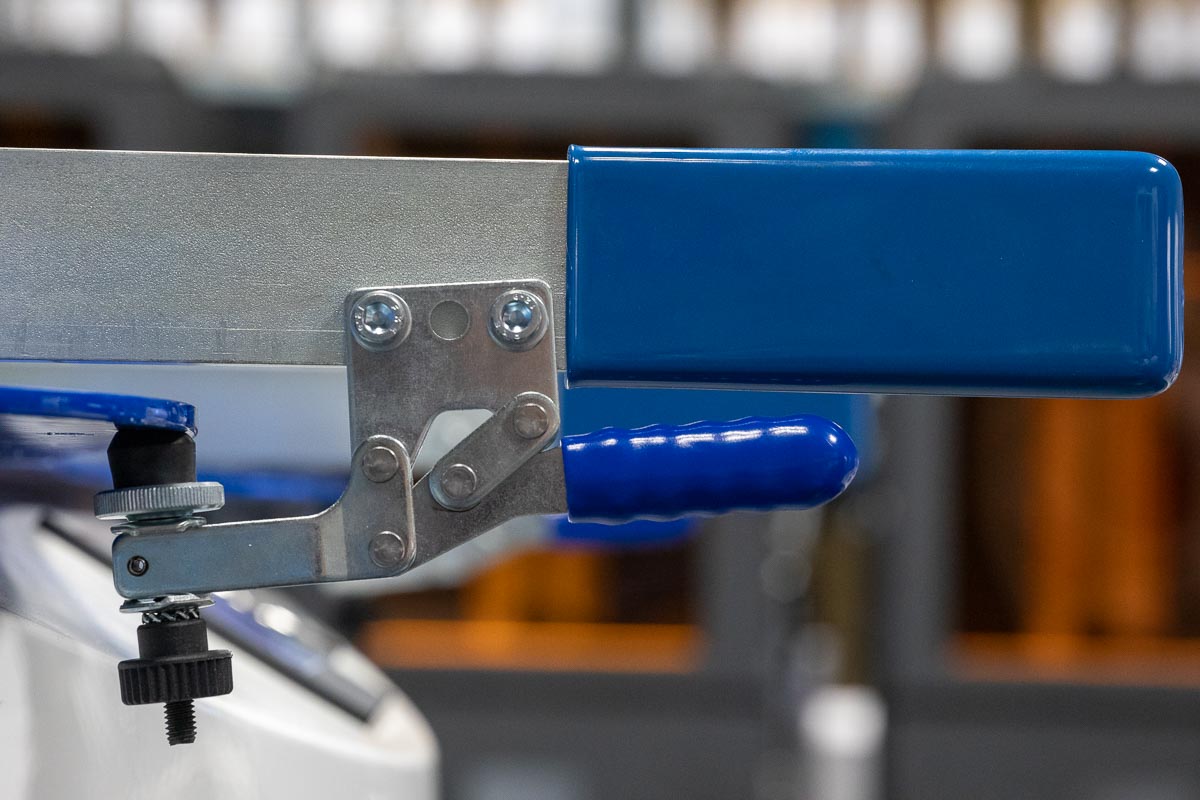
Max part size: 650x620x300 mm
Max material thickness: 6mm
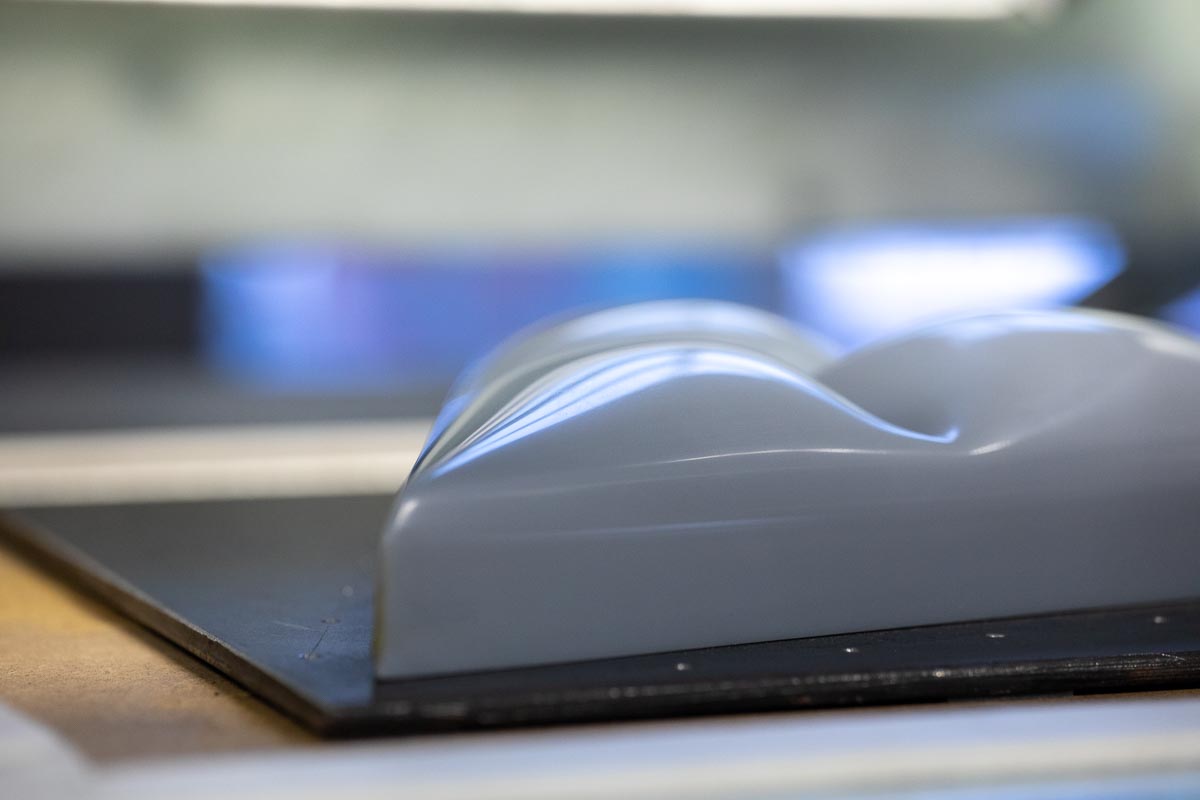
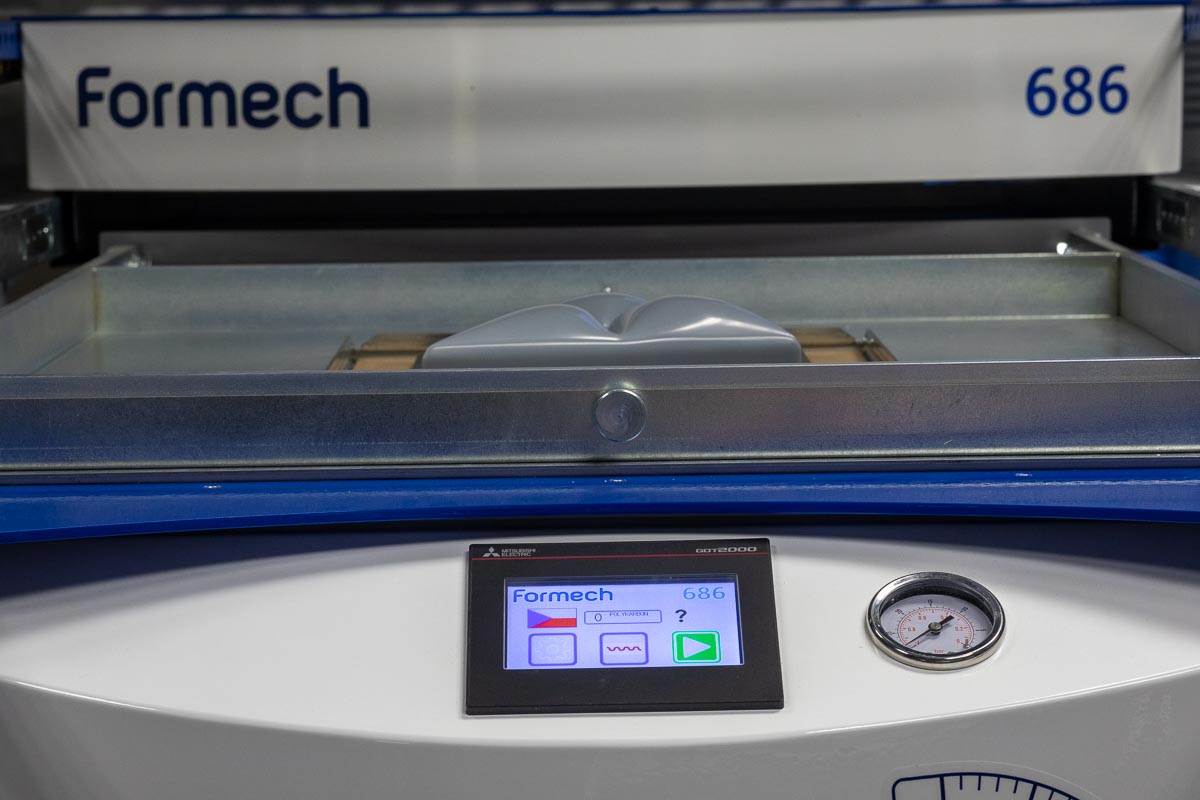
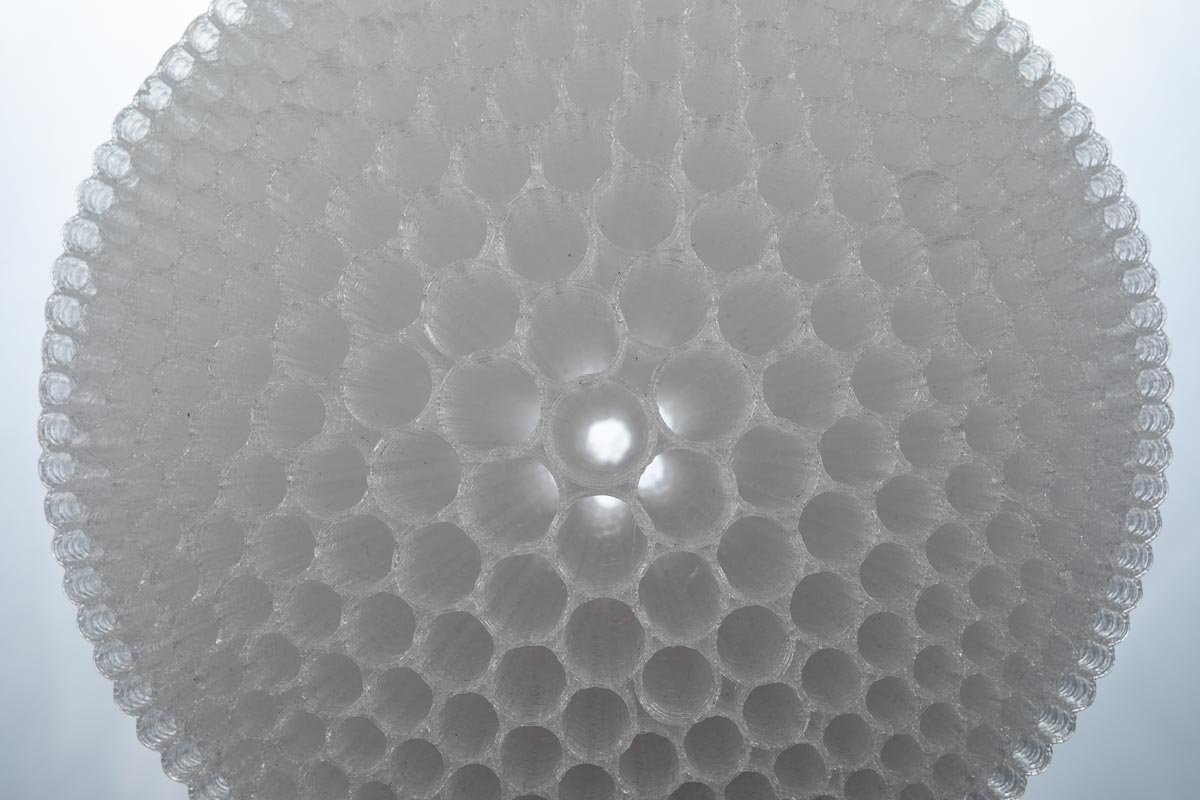
LASER CUTTING
Cut or engrave sheet materials
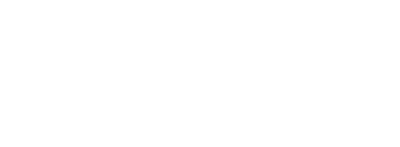
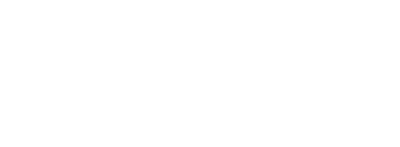
materials cut & engrave
ABS
Nylon
PVC and other thermoplastics
Wood
Cork
Textiles
Paper
Leather
Rubber
Foam
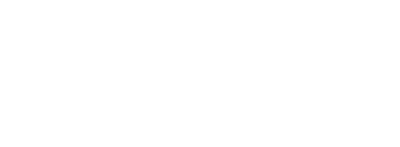
materials engrave
Stone
Steel
Aluminium
Ceramic
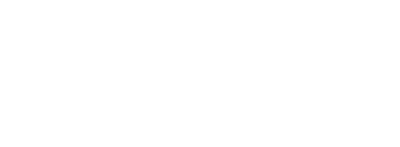
ROBOT ASSISTED LASERCUTTING
Cut or engrave in 3D space
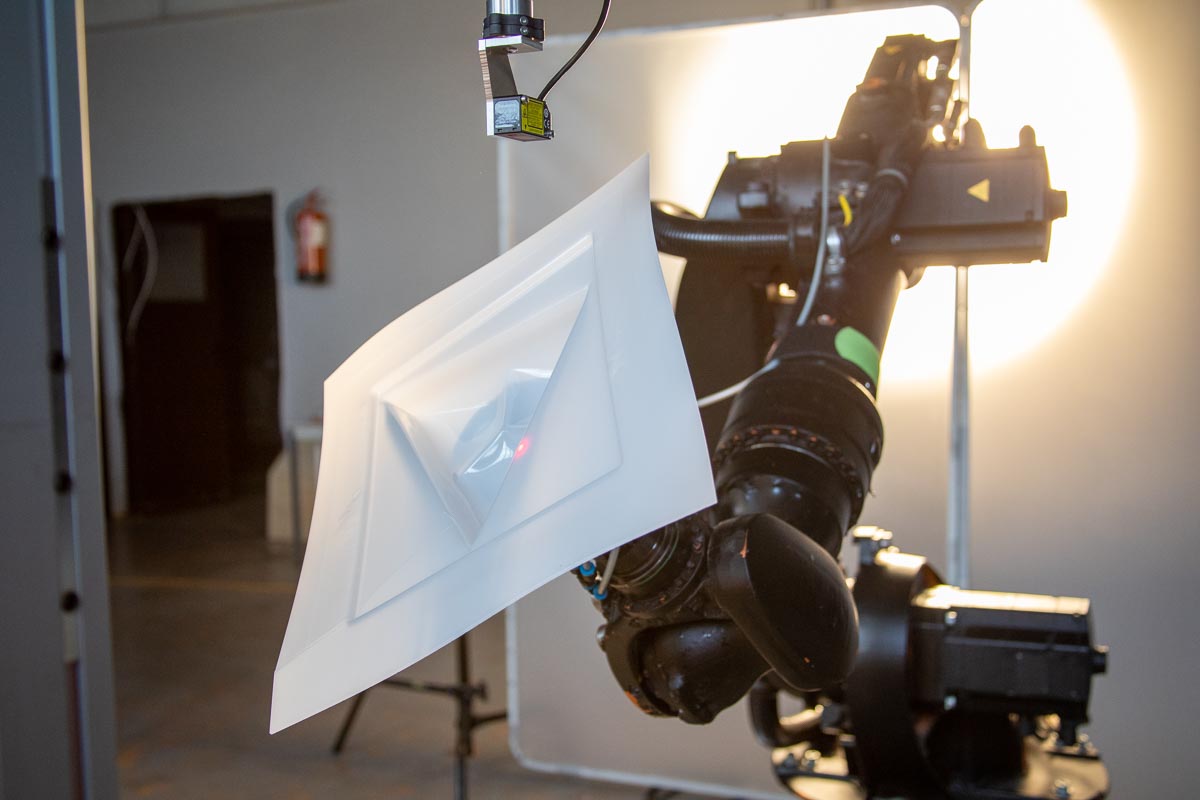
Versatility
Robotic laser cutters can achieve very high precision and can cut at exceptionally high speed. Due to this property, robotic laser cutting is very useful for any type of cutting which needs more accuracy or which is more complex.
Laser fixed - moving parts on Robot for most complex cutting shapes
VACUUM CASTING
No air, no bubles, cast transparent objects cryctal clear
Vacuum casting is one of the most cost-effective ways to produce high quality, low volume plastic parts which can be similar to injection moulding parts
Max mold size 400x400x400 mm, Volume 1 liter
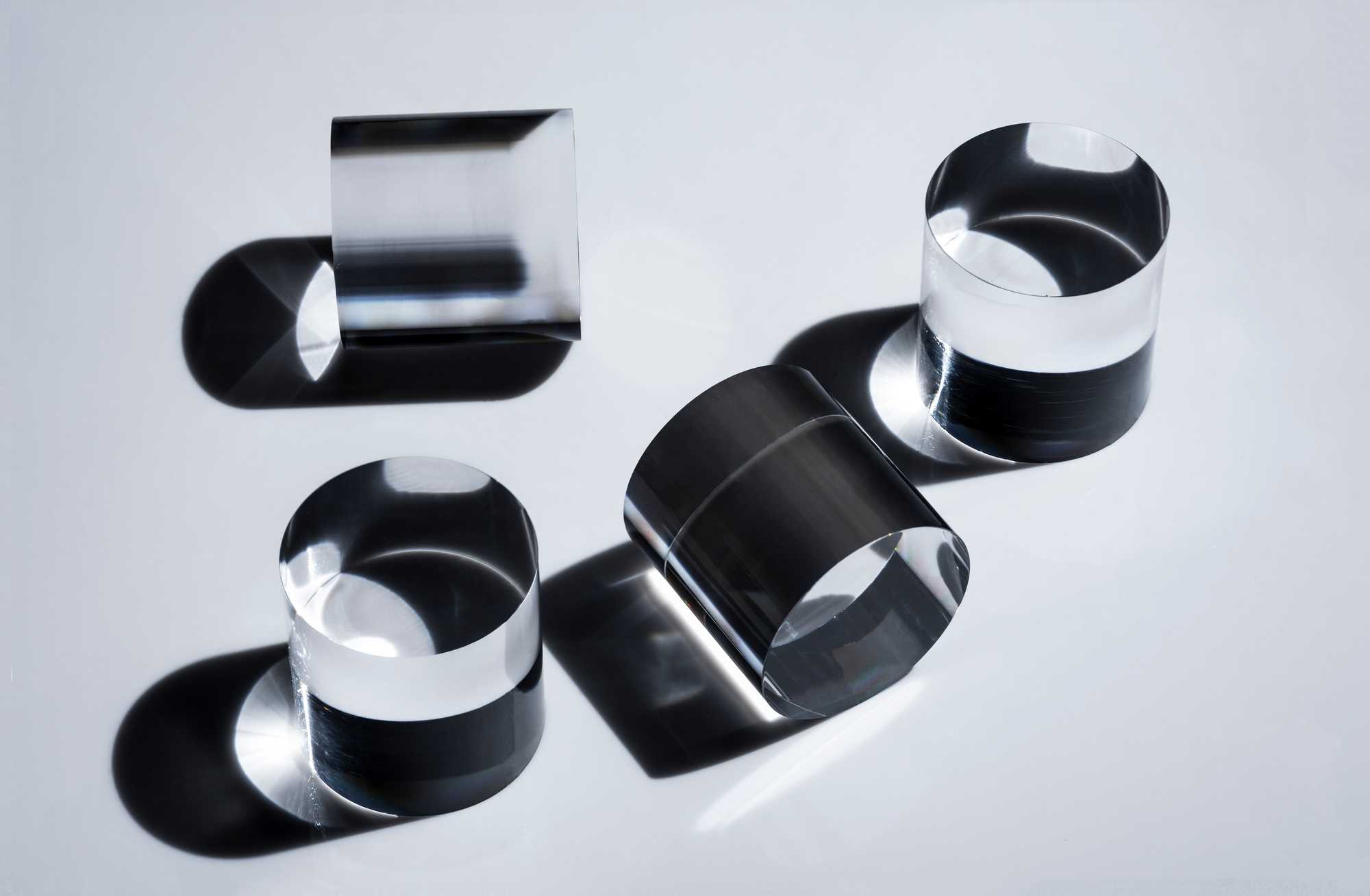
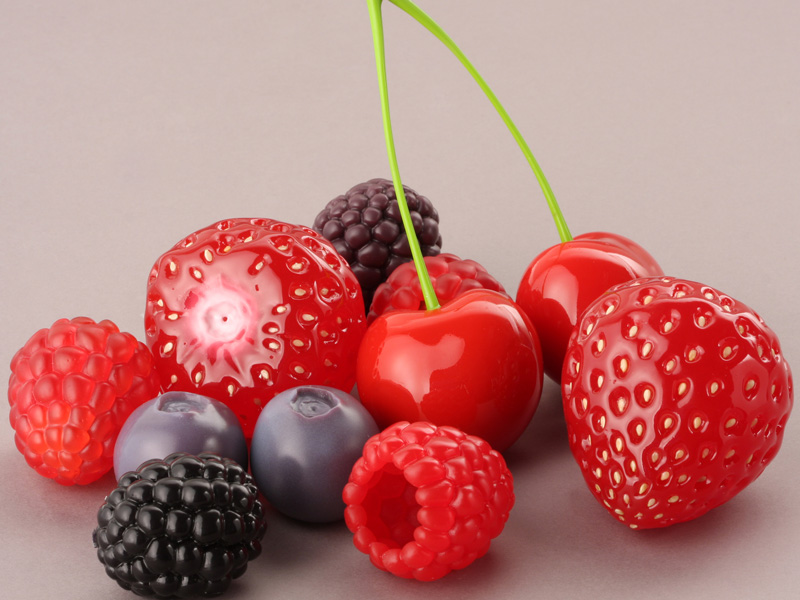
CASTING
Create multiple copies from a mold
Low Cost Urethane casting for parts up to 1000x1000x500 mm.
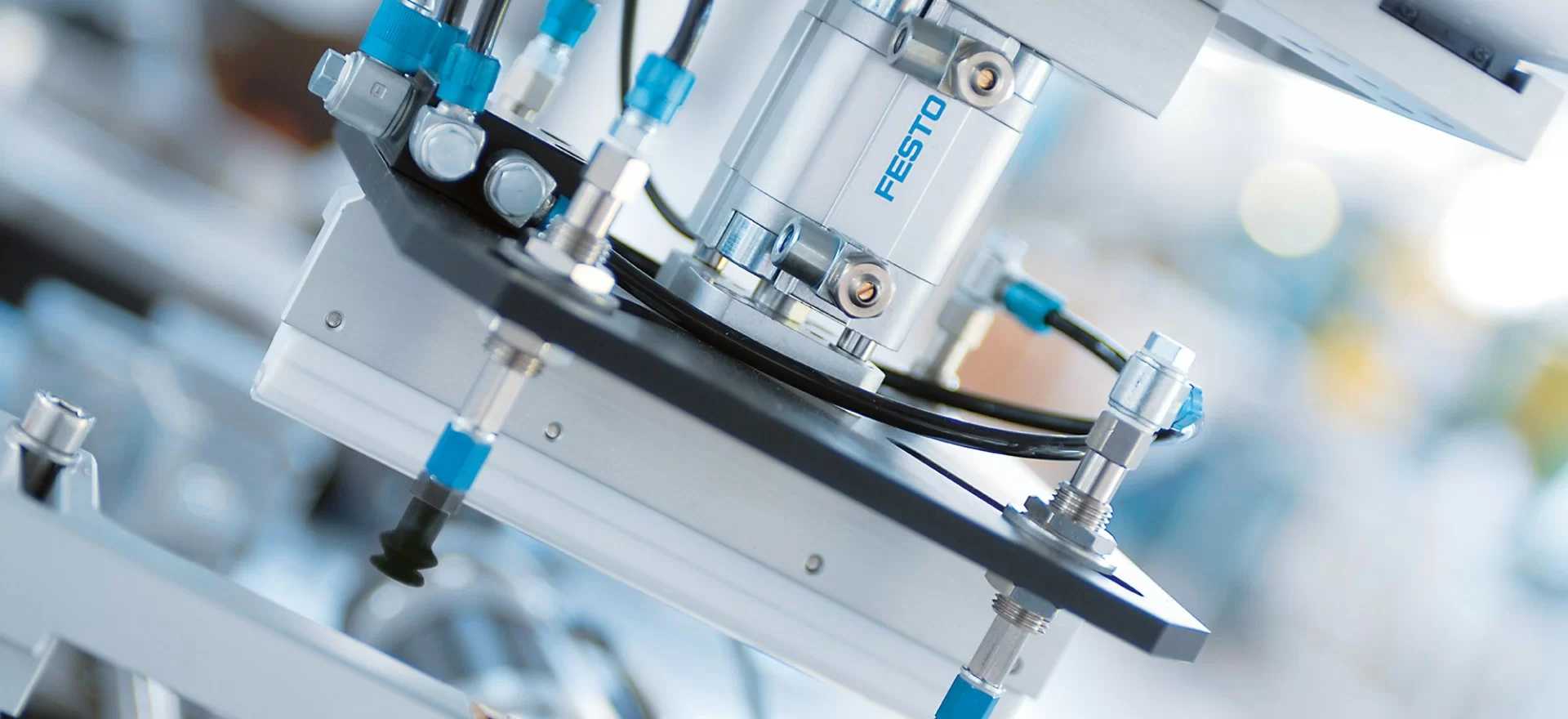
Prototype integration
with Pneumatics, Motors, PLC
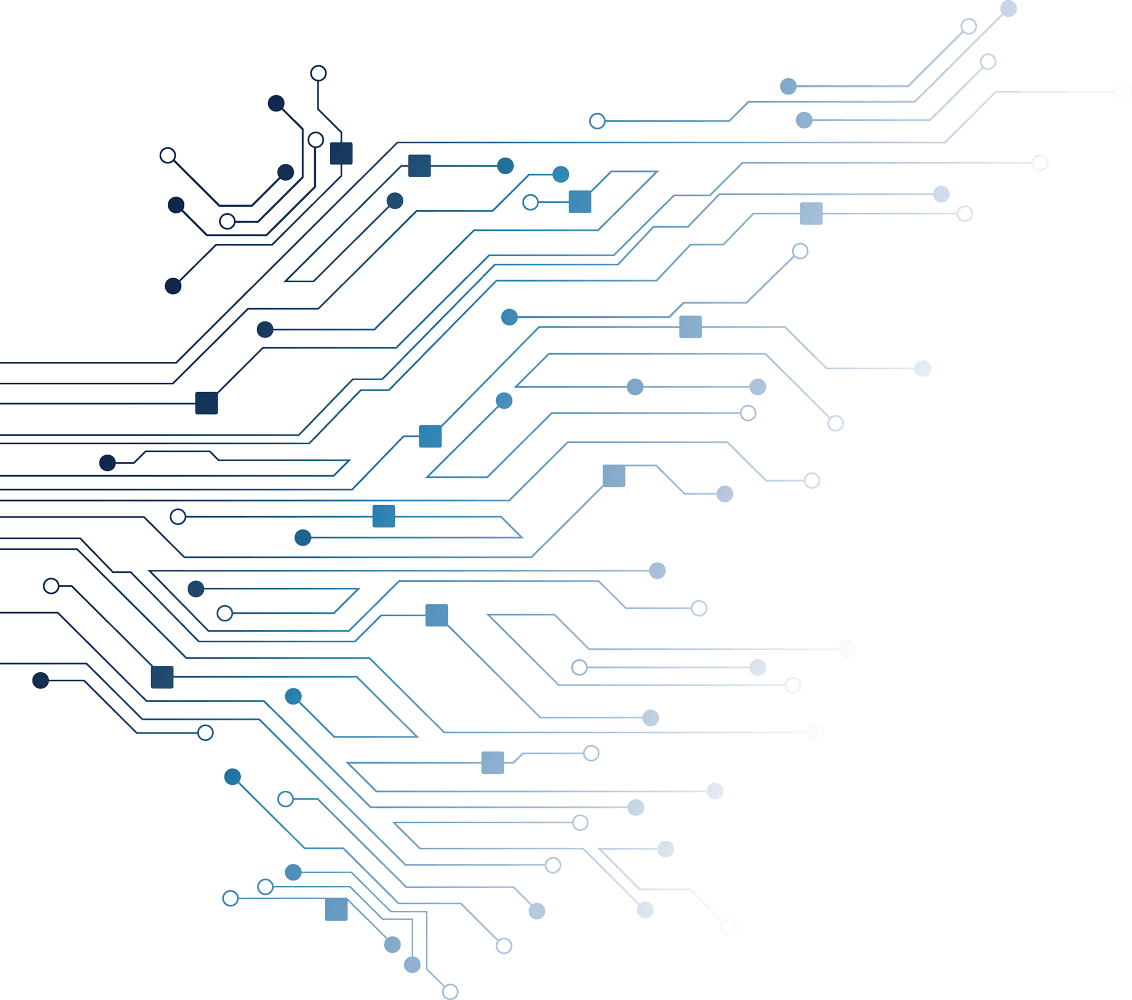
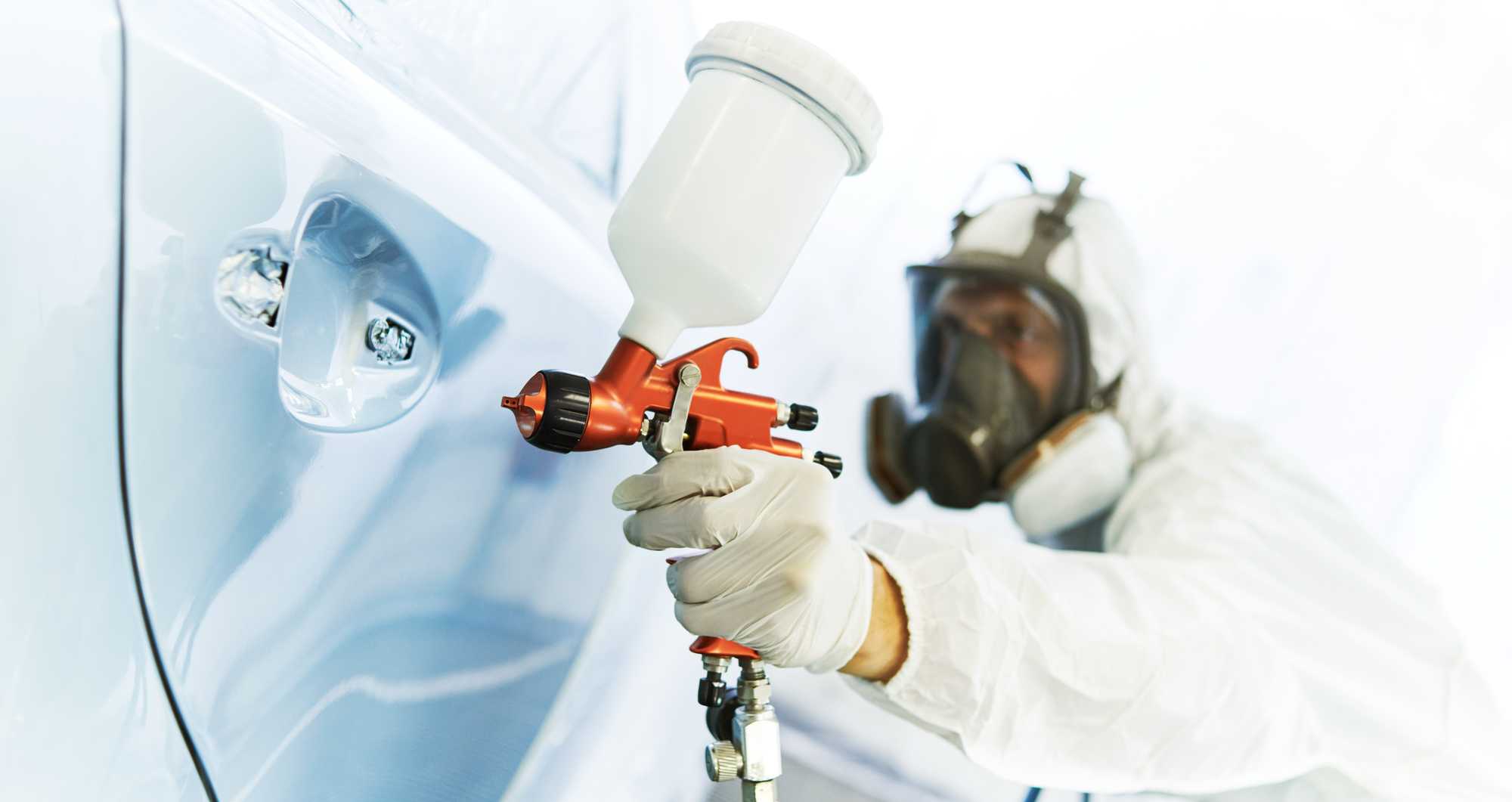
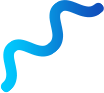
FINISHING
Final touch to your parts
Surface treatment is an additional process applied to the surface of a material for the purpose of adding functions such as rust and wear resistance or improving the decorative properties to enhance its appearance. .
Need a project?
To make requests for further information, contact us via email or phone.
- We just need a couple of hours!
- No more than a working day since receiving your quote and timing